Sustaining Change: How Industrial Leaders Ensure Long-Term Impact
Why Change Doesn’t Stick—and How to Fix It
For industrial companies in oil & gas, energy, mining, and pulp & paper, digital transformation is more than just an upgrade—it’s a fundamental shift in how operations run. Yet, even when new technology is implemented successfully, many organizations struggle with a common challenge:
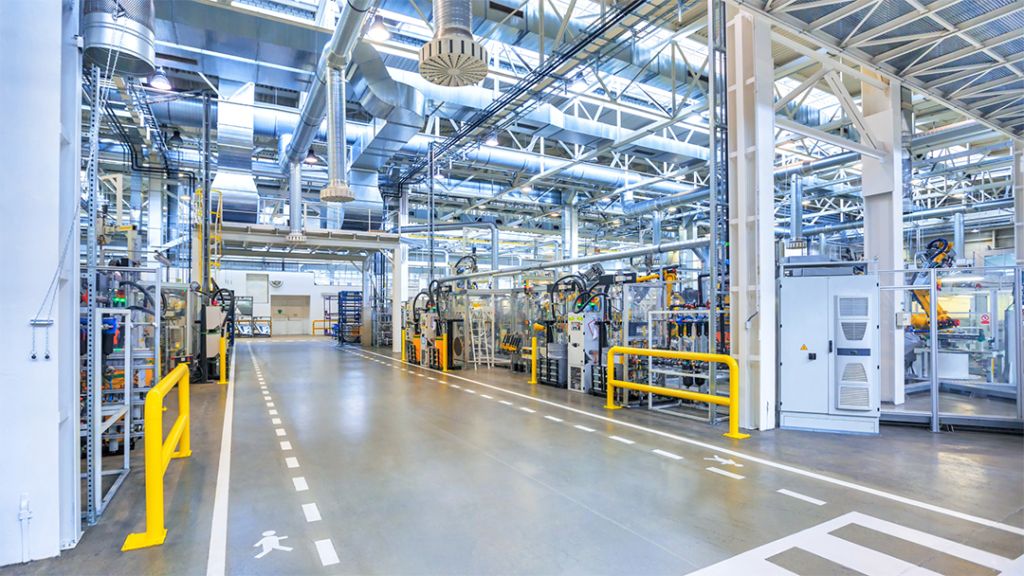
The Change Fades
Employees revert to old habits. Workarounds emerge. Expected efficiencies never materialize.
This isn’t a failure of technology—it’s a failure of sustainment.
The real measure of success in digital transformation isn’t just getting to “Go-Live”—it’s ensuring that the change is fully embedded, embraced, and sustained over time.

The Risks of Failing to Sustain Change
1. Backsliding to Old Ways of Working
When employees don’t see consistent reinforcement of new systems and processes, they naturally revert to familiar routines.
Case in Point: A global energy company launched a predictive maintenance system designed to cut unplanned downtime. Operators initially adopted the tool, but within six months, usage dropped by 40%. Without regular coaching and accountability, frontline teams fell back into manual monitoring, losing the efficiency gains the system was designed to deliver.
Key Takeaway: Change doesn’t sustain itself—leaders must actively reinforce and monitor adoption.
2. Loss of Competitive Advantage
When companies fail to sustain transformation efforts, they risk falling behind competitors who successfully integrate change into their culture.
Case in Point: A mining company invested in an advanced data analytics platform to optimize production. However, leadership engagement waned, and no clear metrics were set to track sustained adoption. Meanwhile, a competing firm fully integrated the same technology, continuously trained its teams, and gained a significant operational edge.
Key Takeaway: Technology alone doesn’t create competitive advantage—ongoing change management does.
3. Unnecessary Rework and Costly Retrofitting
A poorly sustained change often results in partial adoption, leading to costly adjustments or re-implementations.
Case in Point: A pipeline operator invested in a centralized control system but neglected long-term change sustainment strategies. As a result, regional teams continued using outdated methods, forcing leadership to relaunch the initiative two years later—incurring double the cost and delaying efficiency gains.
Key Takeaway: Change sustainment must be a built-in phase of every transformation strategy.

How Industrial Leaders Sustain Change for the Long Term
To avoid these costly pitfalls, leading industrial organizations follow a structured sustainment framework:
1. Align Leadership with Measurable Accountability
Change success starts at the top. Leaders must not only approve digital transformation initiatives but also actively support and reinforce them over time.
Actionable Step: Assign clear accountability measures for leadership, ensuring they drive adoption beyond “Go-Live”.
2. Establish Continuous Learning & Support Systems
Training shouldn’t end after implementation. Organizations that sustain change integrate continuous learning into daily operations.
Actionable Step: Implement ongoing coaching, microlearning, and peer-led training to keep teams engaged.
3. Embed Change into KPIs and Performance Reviews
If change isn’t measured, it isn’t managed. Industrial leaders tie adoption metrics to operational KPIs.
Actionable Step: Set clear performance benchmarks that track system usage, efficiency improvements, and workforce engagement.
4. Foster a Culture of Adaptability
Organizations that sustain change build resilience into their culture, making adaptability a core competency.
Actionable Step: Establish a cross-functional Change Champion network that continuously assesses adoption challenges and implements course corrections.
Final Thought: Sustainable Change is the Real Transformation
Industrial digital transformation doesn’t stop at Go-Live—it’s a continuous process that requires ongoing leadership, engagement, and reinforcement.
The good news? You don’t have to navigate this alone.
On May 7, Dexcent and a panel of industry experts from Enbridge, Colonial Pipeline, ProSci, and Plant.Digital will share real-world strategies for ensuring long-term digital transformation success.
Reserve your spot today: Register for the Webinar
Learn how to turn short-term change into lasting operational excellence.