The Hidden Costs of Poor Change Management in Industrial Operations
The Overlooked Risk That Can Sink Your Digital Transformation
Industrial leaders in oil & gas, energy, mining, and pulp & paper understand the stakes when it comes to digital transformation. Yet, 70% of digital transformation initiatives fail—and poor change management is often the culprit.
When organizations focus purely on technology implementation and ignore the people factor, the hidden costs start piling up:
- Operational inefficiencies caused by poor adoption of new systems.
- Increased downtime from employees struggling to adjust to new processes.
- Low workforce morale and high turnover due to unclear communication and lack of leadership support.
- Rework and compliance failures from resistance and misalignment across teams.
The cost of neglecting change management is not just financial—it’s cultural, strategic, and operational. Without the right change management approach, even the best technology investments fail to deliver long-term impact.
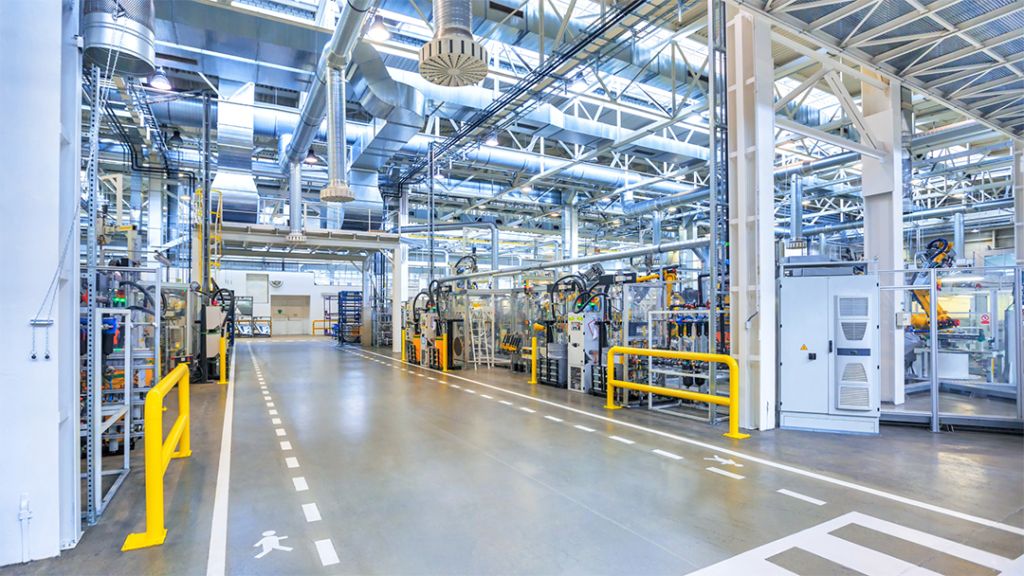
The Real Price of Poor Change Management
1. Unplanned Downtime and Productivity Losses
When employees aren’t properly equipped to embrace new technology or processes, downtime skyrockets.
Case in Point: An oil refinery invested millions in a new asset management system but failed to engage frontline operators in the transition. The result? Operators defaulted to old workflows, leading to costly manual workarounds and extended outages.
Insight: Change adoption is not automatic—it must be actively managed through structured communication, training, and reinforcement.
2. Lost Talent and Employee Resistance
Industrial organizations face a knowledge drain when employees resist change—or worse, leave altogether.
Case in Point: A mining company introduced a new data analytics platform but failed to communicate its benefits clearly to operators. Employees saw it as a threat to their job security rather than a tool to improve their workflows. Key personnel left, taking critical knowledge with them, delaying adoption and forcing the company to hire and retrain new staff at a high cost.
Insight: Change without buy-in breeds resistance. Employees must understand why a change is happening and how it benefits them directly.
3. Regulatory Compliance Risks
In highly regulated industries like oil & gas and energy, compliance failures can lead to fines, legal issues, and reputational damage.
Case in Point: A power generation company introduced a new environmental compliance reporting system but failed to properly train plant managers. The result? Inaccurate data entries and missed regulatory deadlines, triggering audits and penalties.
Insight: Compliance requires consistent training, clear communication, and leadership alignment. A well-structured change management approach ensures regulatory standards are met without disruption.
4. Rework and Project “Do-Overs”
Poorly managed change often leads to failed implementations—forcing companies to redo projects at significant cost.
Case in Point: A pipeline operator invested in a centralized control system but underestimated the cultural shift required. Operators at remote sites resisted the change, continuing with legacy processes. The result? The project had to be restarted, doubling costs and delaying efficiency gains by two years.
Insight: Rework is expensive. Investing in proactive change management prevents wasted time and resources.
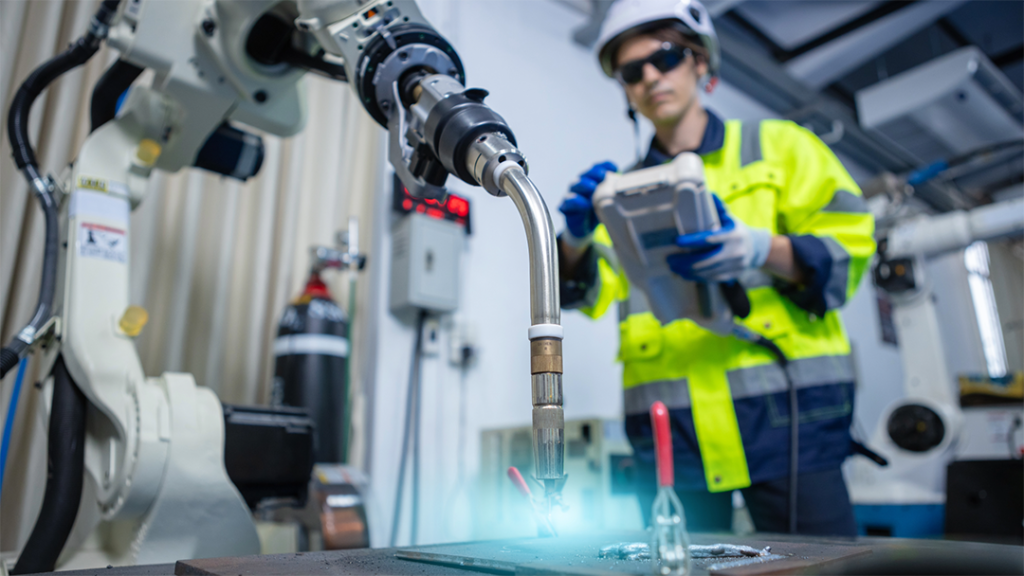
How to Avoid These Pitfalls: A Change Management Framework That Works
1. Align Leadership from Day One
Digital transformation isn’t just an IT initiative—it’s a business-wide shift. Leaders must champion the change, not just approve the budget.
Actionable Step: Clearly define leadership roles in the transformation process. Provide executives and middle managers with the tools to communicate the vision effectively.
2. Engage Employees Early and Often
Employees who feel heard and involved are more likely to embrace change.
Actionable Step: Conduct stakeholder impact assessments. Identify key influencers within your workforce and turn them into change champions.
3. Provide the Right Training—at the Right Time
One-size-fits-all training doesn’t work. Employees need ongoing, role-specific training to feel confident using new systems.
Actionable Step: Move beyond traditional training sessions. Implement on-demand microlearning, real-world case studies, and peer mentoring programs.
4. Measure and Sustain Change Over Time
Change doesn’t end at Go-Live. Continuous monitoring and adaptation are required to ensure long-term adoption.
Actionable Step: Set clear success metrics for adoption, proficiency, and impact. Conduct post-implementation reviews and gather feedback regularly.
Final Thought: Change Management Is a Strategic Imperative
Industrial digital transformation isn’t just about technology—it’s about people. Without a structured change management approach, even the most advanced tools will fall short of their potential.
The good news? You don’t have to navigate this alone.
On May 7, Dexcent and a panel of industry experts from Enbridge, Prosci and Plant.Digital will share real-world change management strategies that drive measurable, lasting results.
Reserve your spot today: Register for the Webinar
Don’t let change failure become a costly reality—learn how to lead transformation with confidence.